Welcome to the
WEMPEC Restricted Site
Content on this site is restricted to current WEMPEC members, faculty, staff and students. You are free to download content from this site, however you may not distribute without express permissions from WEMPEC.
Please reach out to admin@wempec.wisc.edu with questions.
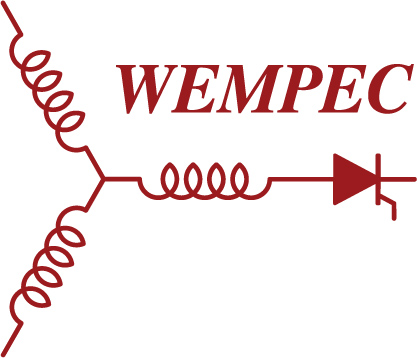
Soon to Graduate Students
Follow link to view list of upcoming student graduations.